FAQ
Get Answers
Typically, all interior work is iron. For the exterior, an aircraft-grade aluminum is predominant, especially at the shore. We also work with bronze, brass, stainless steel, and other exotic metals.
Iron has great strength and rigidity, but solid aluminum has almost the same characteristics, along with anti-corrosive properties. If iron gets scratched with a snow plow or shovel, beaten with a baseball bat, or its coating breaches for any reason, its natural reaction is to start to corrode. With the exception of the shore, we never have to worry about aluminum corroding, ever!
The real “wrought iron” was a soft fibrous metal with a very low carbon content. It would only patina and not “rust to death.” With the invention of the Bessemer steel process in 1888, steel became more available, but it had a higher carbon content. It took decades to gain traction in the market, but because of Andrew Carnegie and others like him, the steel industry was streamlined and the cost of making steel dropped. Steel began to replace the demand for wrought iron. Wrought iron regained popularity into the 1920s when America’s most famous artist blacksmith, Samuel Yellin, did all of his incredible work, which is still sought after and admired today. The 1930s saw the demise of wrought iron. In 1930, steel was expensive and wrought iron was cheap, but by 1940, wrought iron was expensive and steel was cheap. Today, real wrought iron can still be found. It‘s typically re-smelted from British pig iron into the desired shapes, but it is much more expensive.
This varies depending on the complexities of the project. Straightforward terrace railings or wrought iron balcony railings can be done in a matter of two to four weeks. The same goes for typical estate gates. However, for an intricate foyer railing or estate gate where custom tooling or dies have to be created, it can be three to six months.
The Ironworks Consultation Agreement or ICA provides you with our experience and artistic sensibilities, our in-depth knowledge and national connections, as well as resources and vendors, in an effort to help you unearth what is the best fit for your project. There is a fee attached to this service, which is usually credited to your project at completion of the consultation.
Because we cater to your specific needs, design, color, size, and build to your specifications, it would be impossible for us to have everything in stock. We do not begin a project until we have captured your design sensibilities. This enables us to keep our overhead down and create works of the best quality at a fair price.
We have compiled Design Guides of different aspects of our work over the years. You can browse photos and illustrations for guidance and inspiration for your or your client’s needs. This extensive collection of projects always has at least one style, sometimes two or more that align with individual design interests.
For iron, we definitely recommend hot-dip galvanizing plus powder-coat. The DOT rates this life expectancy for 125 years. We feel that is somewhat unrealistic and put the expectancy more towards 50-75 years. But if the coating is scratched or jeopardized, it is not uncommon to have a little weeping in some areas. Without the hot-dip galvanizing procedure, the life expectancy is more like 20-30 years before you see any massive failure, though you might notice some weeping here and there from inside corners. We are currently running long-term tests in a salt spray chamber that accelerates the harsh elements that cause corrosion. We now have data for up to 22 years at the shore with absolutely no delamination.
Pretreatment is the preparation of metal before any finish is applied. It is a very important part of your finish’s longevity. Many people are under the assumption that powder-coat is durable and it is! But it is only as good as the pretreatment. The first, and by far, most important, step is the sandblasting, where all dirt, oils, organic matter, and mill scale are removed. This etches the surface and opens pores in the metal for the powder-coat to bond. The next step is a hot phosphate wash, followed by, not one, but two clean water rinses. For shore projects, a salt spray chemical sealer is applied and is then ready for powder-coating.
First the entire project is coated with a resilient primer and then passed through the oven to bring all parts to 200ºF. With the powder-coat application being an electrostatic process, corner and cavity coverage is minimal, due to the Faraday Cage effect. By having the parts hot, we can overcome that hurdle and apply coverage into those areas much more easily. A third coat is then applied and the piece takes a long slow passage through the curing oven to harden the finish.
You can have practically any color you wish. Even black comes in a variety of sheens, such as Gloss, Semi Gloss, Matte and Flat. We can also custom-blend colors to give your project a signature color. The five most popular colors in our line are Semi-Gloss Black, Matte Black, Flat Black, Statuary Bronze, and Runyan Bronze. You can also pick up colors from your windows, trim, or siding. We recommend that you go with a darker color, which has less tendency to show dirt and transposes the iron character more accurately.
We can easily and economically service anything within a three-hour radius of Compass. This working radius allows us to provide all our services; from on-site visits, to measurements, to installation, within a day’s commute.
However, though we primary service the north eastern USA, we do provide our services all over the nation and internationally on a case by case basis.
While we can provide expert advice and guidance in our area, suggesting best practices, best techniques and sharing the inside track on ironworks, having professional design input is a great benefit. This ensures all areas of the property are in aesthetic harmony.
Solid iron bars are 97.7% recycled content; the 6061 aircraft-grade aluminum is 100% recycled content. The powder-coat finish process emits no Volatile Organic Compounds into the atmosphere like traditional paint does. In addition, the application process is 99.99% reclaimable, which means virtually no loss from overspray.
An independent laboratory performed a salt spray chamber test known as ASTM B-117. The normal test is for 500 hours. Our in-house process did 2,750 hours with flying colors. In an effort to further elevate quality perimeters, we now have an in-house salt spray chamber. We added UV exposure and temperature fluctuation to enhance the stringency and accelerate the testing. There are currently about 25 pieces of various processes and metals undergoing testing to guide us in providing the best possible value for our clients.
Absolutely. We recognize that exceptional properties have exceptional design talent as a core team. This team, in turn, selects talent in each trade to work under their direction, while providing their unique skill sets to the project. The entire sum can be greater than the parts. We all know exceptional properties that offer testimony to that, such as Nemours, Breakers, and Whitehall, to name a few.
The production fence and railing industry has given aluminum as a custom product a bad reputation. These are typically built with hollow pickets and minimal coverage from a glossy powder-coat. The industry goal is purely driven by price. Gloss powder can be bought for $2-$3 per pound, so that is the direction the industry takes. This creates the perception that gloss is aluminum, and flat or matte is iron. Flat or matte powder is typically twice the cost. For us, no matter what material we use, the process is the same: solid pickets, solid welds, and consistent caprail profile. In aluminum, there are challenges not associated with iron, so the cost of creation is slightly higher as is the cost of material, making the end cost 15-20% higher. According to studies we have run at consumer events, flat or matte powder-coat is visually impossible to distinguish.
There are many inexpensive castings available on today’s market, which contain cheap fillers such as copper or zinc. These castings, when exposed to shore elements will have a galvanic reaction, just like on a car battery terminal. This reaction will not occur as long as there isn’t any salt element in the atmosphere, which is why these same castings hold up just fine on properties not exposed to shore conditions.
Base 535 is a magnesium-based aluminum that withstands the shore elements. The U.S. Navy specifies 535 on all their marine applications. It has been proven to be a great fit for anything shore-related. The downside to this chemistry is that it is cast at a higher temperature and reacts to the mold it is poured into, picking up more gas from the residual atmosphere. These impurities have to be dealt with prior to finishing. Our protocol is to bake at 600ºF. The perimeter fence of a New Jersey seaside retreat kept out unwanted intruders from this private haven, but just as importantly, it kept burglars away from the families prized art collection. The property fence met all the applicable building codes to prevent accidental death by drowning. However, there was a much bigger challenge.
As in any trade, there are those who will always work for less. They can cut quality, finish or attention to detail, sometimes in half. There are also competitors who charge you thousands more for the same level and caliber of quality and detail that we provide. We really believe in delivering the best quality at a fair price.
Amos, the president of Compass Ironworks, will work directly with you through the ICA, design and budget stages to capture your design vision. Upon project agreement, the design will be reviewed in-office and a craftsman will travel to your site to perform accurate measurements, discuss pertinent details, and get a feel for the project’s installation. He will then be responsible for creating the work. This same craftsman oversees pretreatment and powder-coat and is in charge of the installation. This system works well for direct dialogue and collaboration with your craftsman, similar to the care you might expect from a one-man shop but with the resources and knowledge that a large shop can offer — providing the best value, from a wide range of equipment and expertise, to finish options and longevity. If any challenges arise, Amos is always on hand to ensure the job is completed to your satisfaction.
Yes, we have extensive experience in replicating projects from photos or projects that were done more than 100 years ago. We even replicated a project from England that dated to 1861, and from Italy from 1742. If you know what you like, that is a great start!
Design
Complimentary
Design Guide
Our Design Guide provides a wide portfolio of Compass Ironworks creations. Simply identify designs that you like and give us a call for a no-obligation consultation.
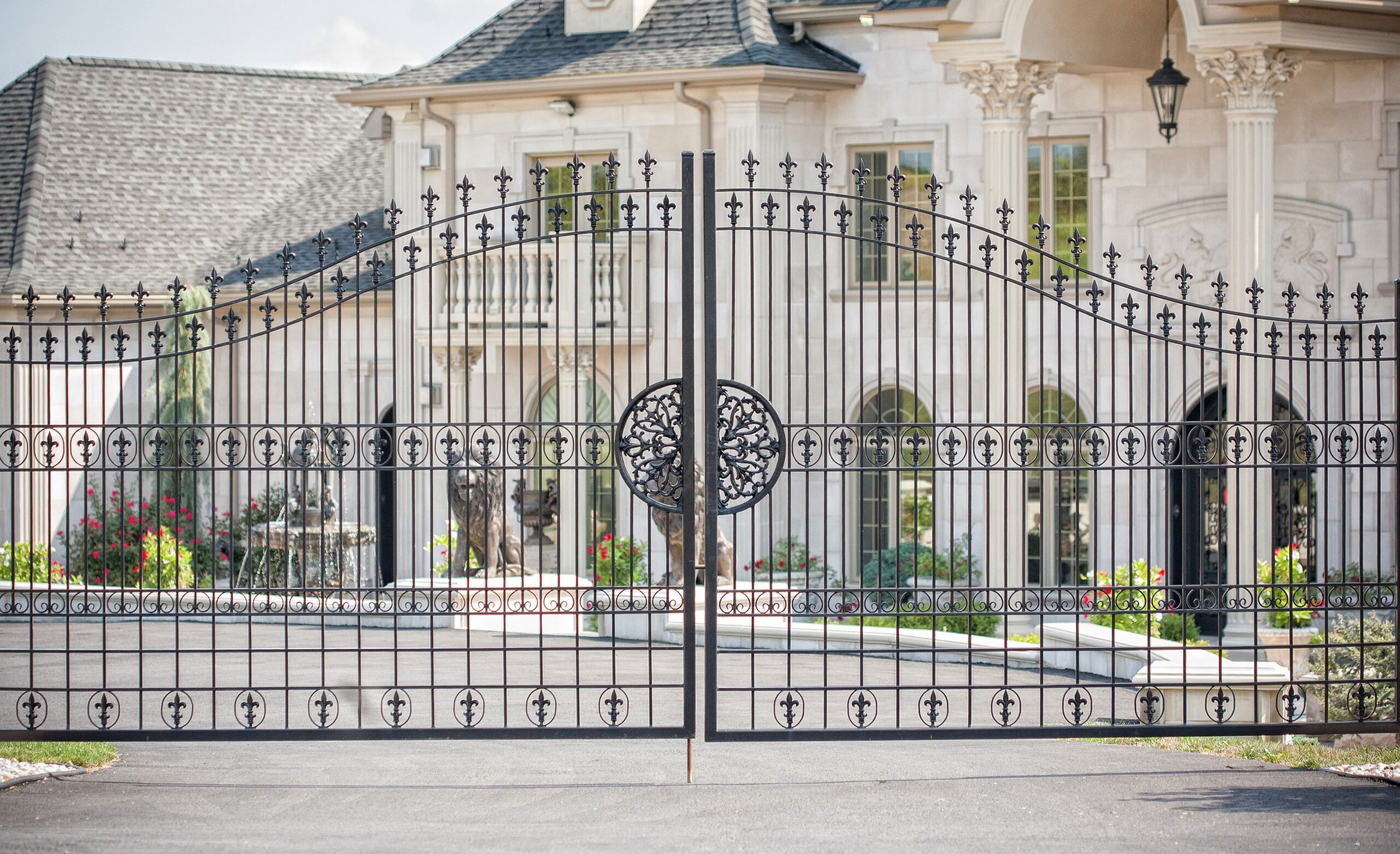