From Wrought Iron to Steel
For centuries, ornamental ironwork was crafted from wrought iron. This material, known for its malleability and resistance to corrosion due to its low carbon content, allowed iron creations to last for decades without rusting. However, with true wrought iron now rare and steel taking its place, we’re seeing ironwork begin to corrode within days. So, what’s the solution? The most effective answer is hot-dip galvanizing.
What is Hot-dip Galvanizing?
Hot-dip galvanizing is highly effective in providing superior corrosion protection due to its multi-step process that creates a metallurgical bonded zinc-iron alloy layer. This zinc layer acts as a fully contained barrier between the base metal and the environment.
How it works!
The process of hot-dip galvanizing ironwork begins with preparing the raw metal through a five-stage rinsing process. Then, the metal is is dipped into a kettle of molten zinc at 835 degrees. The semi-liquid zinc coats not only the exterior, but also the interior walls of all channels, posts, caprails, etc. It also coats the intricate surfaces like scrollwork and collars on iron railings, property fences, and driveway gates.
As we pull the metal out of the molten zinc, it cools and the zinc solution drains. As it cools, a “fudge-like” texture with runs, sags, and icicles will begin to form on the surface of the metal. This creates a distinct textured finish called “spangle,” which gives a new ironwork an old authentic wrought iron texture. Then, after welds are cleaned and imperfections of the galvanizing process are removed, the ironwork is brush blasted and powder coated (or painted) for a lasting finish.
Innate Challenges of Galvanizing Ironwork
Though galvanizing is the best solution for current ironwork longevity, it does not come without its challenges.
Weld Bulging: One challenge with hot-dip galvanizing is that welded areas can develop a “weld bulge” zinc buildup. This approx 1/16″ zinc buildup happens due to the higher silicon content found in the weld. What we do to combat this issues is we expertly smooth the welds before galvanizing. Then, we carefully sand and smooth these bulges down after galvanizing to ensure these welds remain ‘invisible’.
Sags and Icicles: As mentioned above, when zinc solution solidifies, it creates sags and icicles as it drips of the metal surfaces. These imperfections also must be carefully ground down just short of the surface of the parent material, for best aesthetic results.
Outgassing: Among the most challenging issues with galvanized ironwork is the outgassing that can happen during the finishing process of powder coating. This outgassing creates pinholes within the welds and surface areas of the zinc coating. This often times it has to do with the extreme changes in temperature of the zinc and base material, and the escaping moisture that may be trapped in the metal. The accelerated and decelerated temperature change causes moisture or gases to be trapped inside the base metal. When you apply the powder coating to this it sits on top and is held by electrostatic forces. During the curing process, the trapped gases can escape, causing eruptions in the powder coated finish; thus the pinholes. To minimize these issues, we use a specific process:
1.) Place the raw custom iron project in the oven,
2.) Bake it at 400 degrees for 30 minutes, and
3.) While the part is still above 200 degrees, spray the powder coating onto it, allowing it to melt and gel immediately.
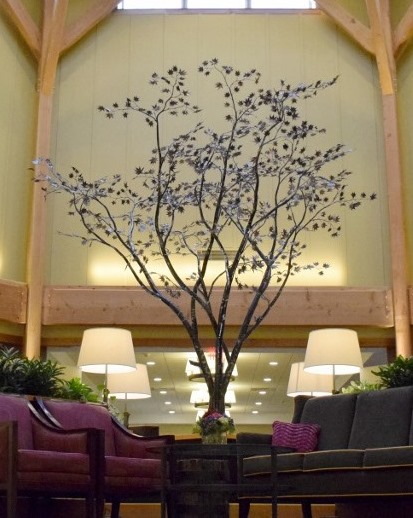
Case Study- Galvanized Metal Trees
One unique thing that we offer at Compass Ironworks are our Artistic Metal Trees. These trees are hand crafted with iron and hot dip galvanized to ensure a long, beautiful life!
With this tree statue, you need to make special provisions. First, it is important to vent all interior spaces so the air can escape as the tree is lowered into the zinc. This allows the inside walls of the trunks and branches to be coated by the zinc. As you hoist the iron tree sculpture out, the liquid drains from the bottom while air enters from the top. These holes will then be plugged with tapered zinc plugs and sanded smooth before powder-coating.
For our duplex finish process, powder-coating is applied on top of the hot-dip galvanized layer; this eliminates corrosion concerns completely. The zinc provides cathodic protection, which in essence, sacrifices itself to protect the base metal structure. Note: Ensuring proper adhesion between the zinc layer and the powder coating is vital. We achieve this by brush-blasting the galvanized surface before powder coating.
When completed, this CIW-2135-I finish can be remarkable. The DOT rates this duplex finish system for up to 120 years with only a 20% failure rate. This finish guarantees both authenticity and longevity for your ‘wrought’ iron designs—whether for exterior custom railings, forged fences, or driveway gates—be admired for generations.
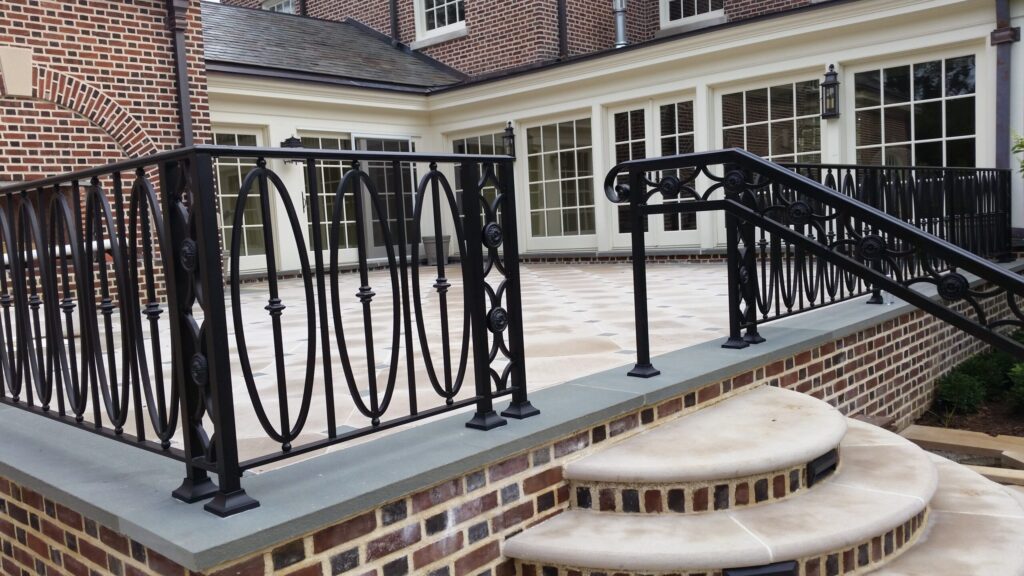